New benchmarks for corrosion protection
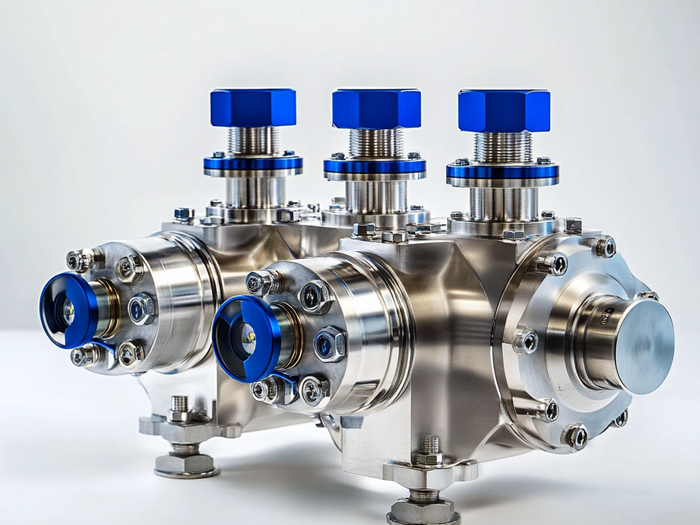
What is gas nitriding and why is it important for high chromium, corrosion resistant steels?
Gas nitriding of high chromium, corrosion resistant steels is an essential process to maximise the performance of these materials. These steels, characterised by high corrosion resistance and strength, play a key role in industries such as medical, aerospace and automotive. But there is a challenge: to nitride the surface of these steels, the protective passive layer must be temporarily broken up without compromising long-term corrosion resistance.
- Process Temperatures: 300–450 °C
- Layer thicknesses: 1–30 µm
- Common materials:
- Martensitic steels: 1.4122, 1.4104, 1.4542
- Austenitic steels: 1.4571, 1.4301
- Ferritic and duplex steels
Challenges in gas nitriding
Gas nitriding of high chromium, corrosion resistant steels faces two major challenges:
- Breaking up the passive layer: The passive layer is formed at chromium contents of 12% and above and protects the steel from corrosion. However, in order to nitride the underlying surface, this layer must be temporarily removed during the process.
- Maintaining corrosion resistance: During heat treatment, chromium can bind nitrogen (to form chromium nitrides) or carbon (to form chromium carbides). This bound chromium is then unavailable to reform the protective passive layer, reducing corrosion resistance.
The RÜBIG solution: Innovative gas nitriding for corrosion-resistant steels
RÜBIG has developed a unique process that temporarily breaks up the passive layer during nitriding and then ensures the formation of a new protective layer. This allows simultaneous nitriding and maintenance of corrosion resistance - all without complex pre-treatments or additional process steps. With this technology, RÜBIG is setting new standards in the treatment of high chromium steels.
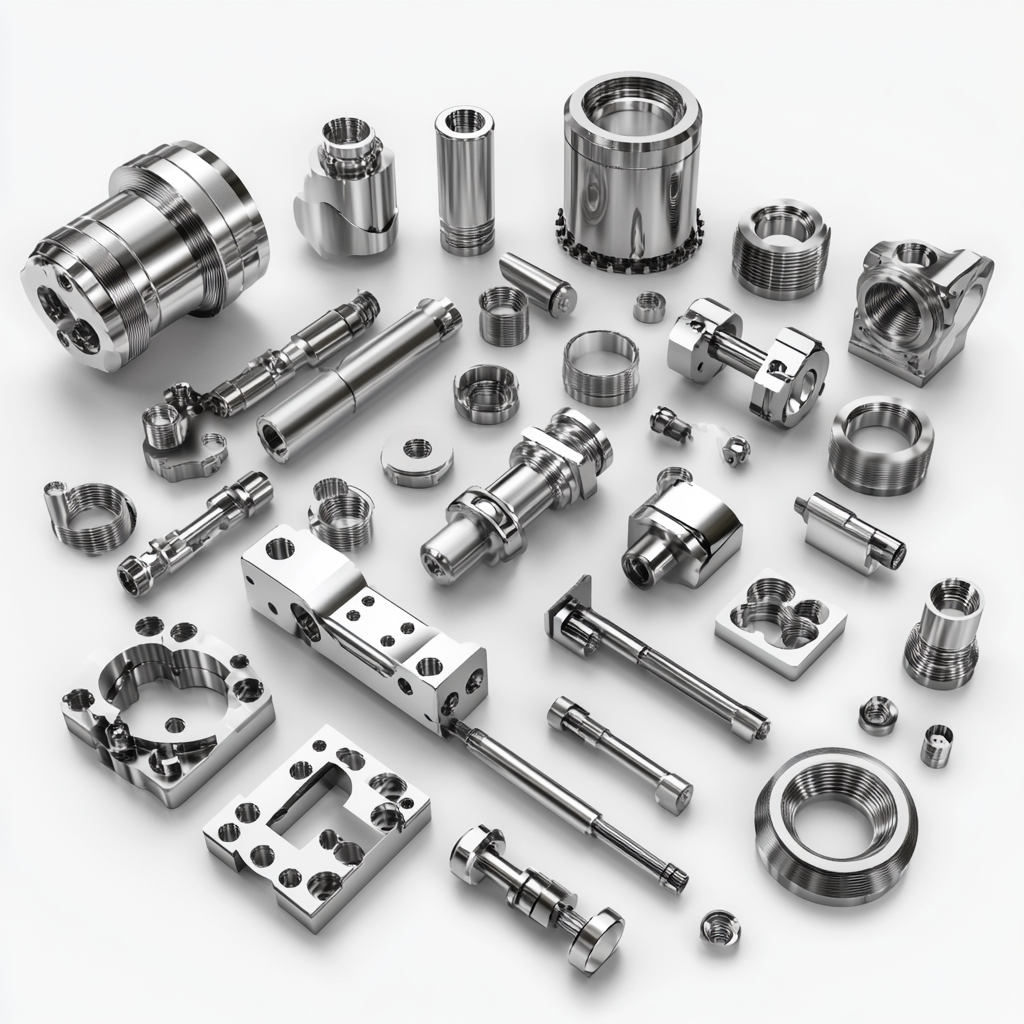
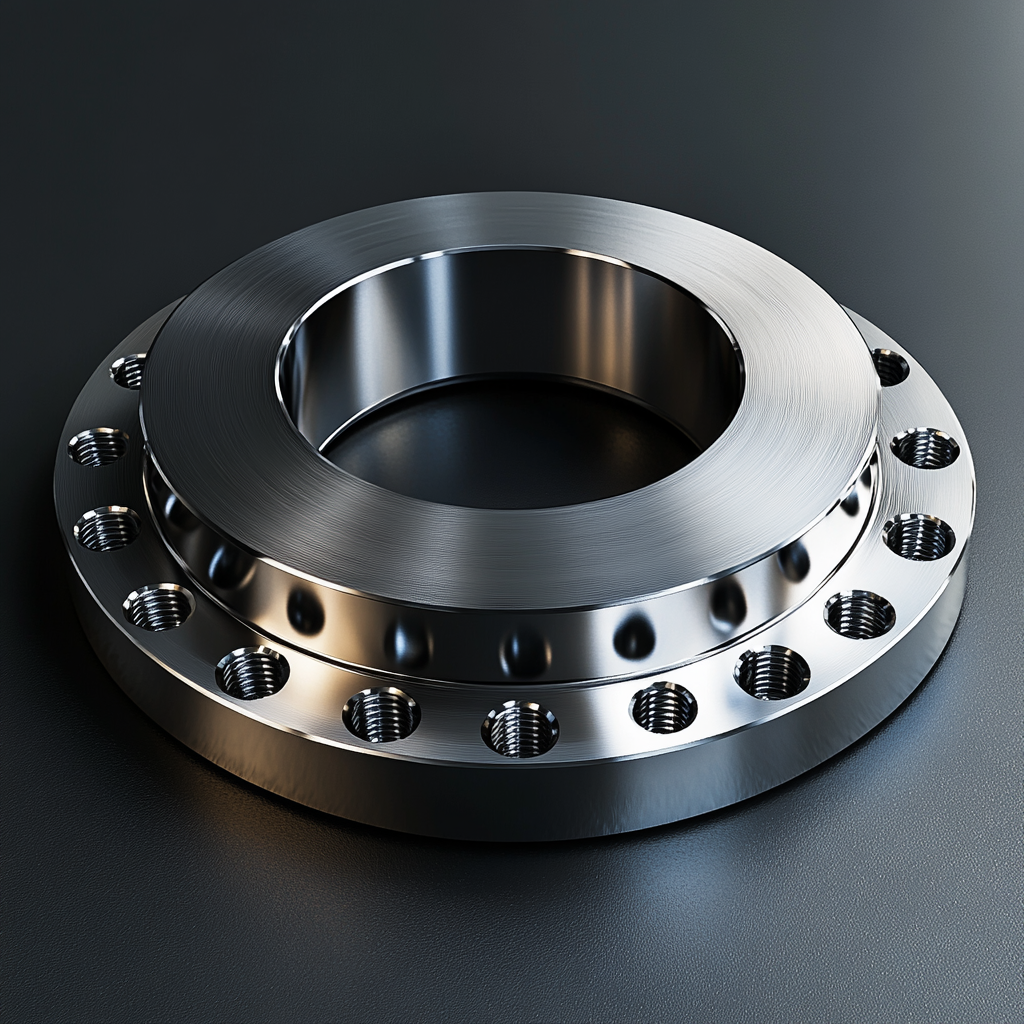
Four main groups of corrosion-resistant steels:
Each of these steel groups presents specific challenges for thermochemical treatment. It is therefore essential to match the process precisely to the properties of the material.
Martensitic steels
- Chromium content: 12–18 %
- Carbon content: > 0.05 %
- Examples: 1.4122 (X39CrMo17-1), 1.4104 (X14CrMoS17)
Austenitic steels
- Chromium content: 17-25 %
- Nickel content: > 8 %
- Examples: 1.4571 (X6CrNiMoTi17-12-2), 1.4301 (X5CrNi18-10)
Ferritic Steels
- Carbon content: < 0.1%
- Chromium content: > 13%
Duplex Steels
- Combination of austenitic and ferritic microstructures
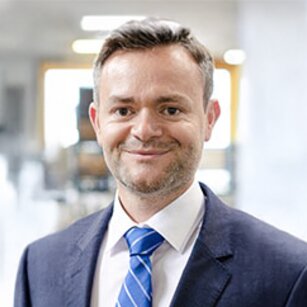
Innovative and Tailor-Made
With over three decades of technological leadership, we develop a system concept that is precisely tailored to your manufacturing processes. Speak with our expert and implement a solution that sustainably optimizes your production.
DI Stefan Haas
Head of Sales
Our Gas nitriding system
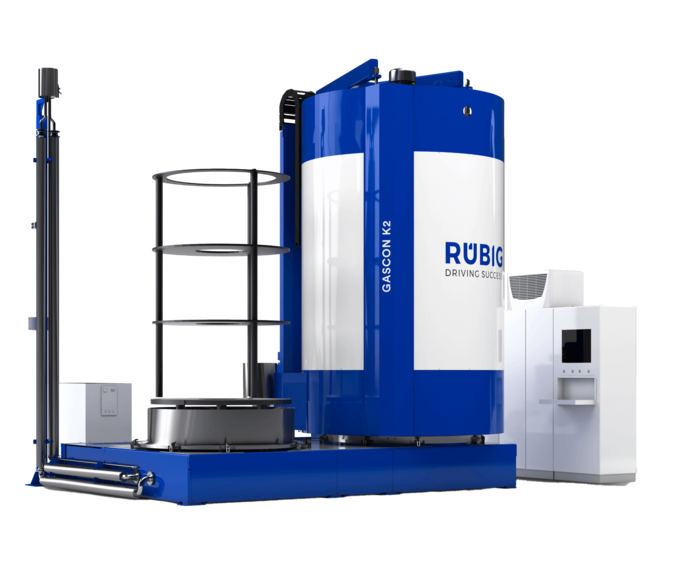
The best choice for gas nitriding high-chromium steels
Gas nitriding of high-chromium, corrosion-resistant steels requires precisely coordinated processes that preserve the special material properties. RÜBIG's innovative technology makes it possible to break up the passive layer in a controlled manner and at the same time ensure long-term corrosion resistance. The RÜBIG GASCON K2 systems set new standards in efficiency and quality.
The most important features of the RÜBIG GASCON K2 systems are
- Treatment temperatures: 300-450 °C
- Layer thickness: 1-30 µm (S-phase, expanded austenite, diffusion zone)
- Layer hardness: 600-1.600 HV
Not only austenitic and martensitic steels, but also ferritic and duplex steels can be nitrided reliably and efficiently with GASCON K2 systems. This makes them the ideal choice for industrial applications.